The importance of ultrasonic level sensors in industrial automation
Industrial automation has revolutionized manufacturing processes, increasing efficiency, reducing costs, and enhancing overall production quality. One of the key components of industrial automation is the ultrasonic level sensor, which plays a vital role in various applications. Ultrasonic level sensors have become an integral part of industrial automation due to their unique capabilities and advantages.
Ultrasonic level sensors utilize high-frequency sound waves to non-invasively measure the level of substances in containers, tanks, or silos. They operate by sending out ultrasonic pulses that bounce off the surface of the material being measured and then capturing the reflected echoes. The time it takes for the sound waves to travel to and from the material's surface is used to calculate the material's level. This measurement is accurate, reliable, and unaffected by many factors that can compromise the performance of other types of level sensors, such as viscosity, density, pressure, and temperature.
One of the primary benefits of ultrasonic level sensors in industrial automation is their versatility. They can be used in a wide range of applications, including but not limited to:
Liquid level measurement: Ultrasonic sensors are commonly used to measure the levels of liquids in tanks, reservoirs, and other containers. They provide real-time data on liquid levels, which can be used to trigger alarms or control processes if levels reach critical levels.
Powder and bulk material measurement: Ultrasonic sensors can accurately measure the levels of powders and bulk materials in silos or other storage facilities. This information is crucial for efficient material handling and process control.
Flow rate measurement: By combining ultrasonic sensors with additional hardware, it is possible to measure the flow rate of liquids or bulk materials. This capability is particularly useful in processes that require precise control of material movement and dispensing.
Voidage measurement: Ultrasonic sensors can be used to measure the amount of voidage or empty space within a container or silo. This information is valuable for optimizing material filling and discharge operations.
Another key advantage of ultrasonic level sensors in industrial automation is their reliability and longevity. Since they operate with non-contact measurement, they are less prone to wear and tear compared to mechanical or electro-mechanical sensors. This translates to reduced maintenance requirements and longer lifespans, which can significantly impact overall operational costs.
Moreover, ultrasonic sensors offer excellent accuracy and repeatability in a wide range of environments. They can operate effectively in challenging conditions such as high pressure, high temperature, or corrosive environments that can compromise the performance of other types of level sensors. This flexibility makes ultrasonic sensors an excellent choice for a wide range of industrial applications.
In addition to their practical applications, ultrasonic sensors also contribute to improving operational safety in industrial settings. By providing accurate and reliable liquid level measurements, they can help prevent potentially dangerous situations such as overflowing tanks or running out of raw materials during production processes. Early warning systems based on ultrasonic sensors can trigger alarms or automatic shutdowns when predefined safety thresholds are exceeded, thus minimizing the risk of accidents or equipment damage.
In conclusion, ultrasonic level sensors play a crucial role in industrial automation, providing accurate, reliable, and versatile measurement capabilities across a wide range of applications. Their non-contact operation, reliability, longevity, accuracy, and adaptability to challenging environments make them an indispensable component of modern industrial processes. As industrial automation continues to evolve, the significance of ultrasonic sensors will likely increase, further enhancing operational efficiency, safety, and overall productivity.
https://www.jxhjbh.com/1950.html
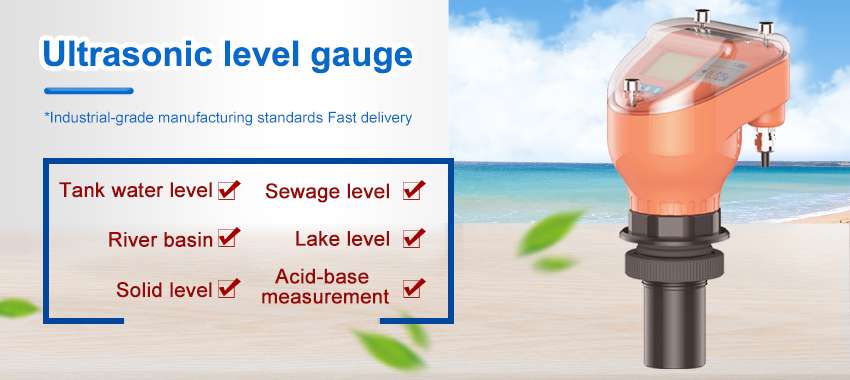